Slip is an important characteristic of an induction motor. Without slip, the induction motor will not be able to perform its allocated task. Slip is the difference between an induction motor’s synchronous and asynchronous speed or the difference between the synchronous speed of the electric motor magnetic field, and the shaft rotating speed. Slip increases with increasing load providing a greater torque.
Torque
Torque, also known as moment of force, is the measure of the energy required to rotate a shaft. Through practical example, lifting a weight similar to the one used in water wells (see figure below). The required force “F” to be applied on the winch depends on the length “E” of the crank handle. The larger the crank handle, the less force is required. By doubling the length “E” of the crank handle, the required force “F” is reduced by half.
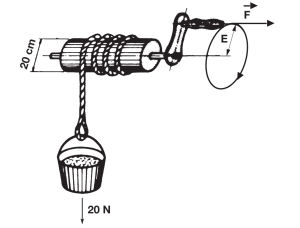
Torque vs Speed Curve
The induction motor has zero torque at synchronous speed. As the load increases, the motor speed will decrease gradually until the torque reaches the maximum value which the motor is capable of developing at normal speed. If the load torque continues to increase, the motor speed will suddenly decrease and may even lock the rotor. By graphically representing the torque variation with the speed for a normal motor.
The torque values relative to these points are specified in the standard IEC 60034-1
- 1. Basic torque, Co
- This is the calculated torque the rated output and synchronous speed.
- 2. Full load torque, Cn
- This is the torque developed by the motor at the rated output at rated voltage and frequency.
- 3. Breakaway torque, CO
- This is the minimum torque developed by the locked rotor for different angular positions of the rotor at rated voltage and frequency.
- This torque can be indicated in Nm or more frequently as percentage of the rated torque.
- In practice, the locked rotor torque should be as high as possible to enable the rotor to overcome the initial load inertia, and quickly accelerate it, especially when started with
reduced voltage. - 4. Minimum torque Cmin
- This is the smallest torque developed by the motor when accelerating from rest or zero speed to the speed corresponding to maximum torque. In practice this value must not be very
low, i.e. the speed torque curve should not have a strong depression during acceleration otherwise starting time is too long, resulting in overheating of the motor, especially in cases
of high inertia, or starting on reduced voltage. - 5. Breakdown torque Cmáx
- This is the maximum torque developed by the motor at rated voltage and frequency, without an abrupt drop in speed. In practice maximum torque must be as high as possible for two reasons:
- The motor must be able to easily overcome loading peaks which can occasionally occur with crushers, calandering machines, mixers, etc.
- The motor speed should not oscillate, i. e., the speed should not drop abruptly when momentary and excessive voltage drops occur.
where:
Co = Nm
P = kW
nS = speed (rpm)
Reference:
Electric Motors Specification Guide - WEG