Contents
I. What is ATEX?
II. Explosive Atmosphere
IV. Equipment ATEX information
V. Equipment Group and Safety Category
VI. Equipment Protection Code
VII. Gas Group
VIII. Sources of Ignition
IX. Temperature Class
X. Equipment Protection Level
I. What is ATEX?
ATEX is an abbreviation for "ATmosphere EXplosible" and is the abbreviated name of the European Directive concerning the use of explosion-proof electrical and mechanical equipment, components and protective systems. It came into force on 1 July 2003, and all new equipment and protective systems have been subject to it since that date.
ATEX refers to two European directives for ensuring safety in areas with an explosive atmosphere. The two ATEX directives are:
- The 'Workplace' Directive (1999/92/EC) provides the requirements for workplace safety, ensuring that workers are protected in environments where there is a risk of explosive atmospheres.
- The 'Equipment' Directive (94/9/EC), recently updated as 2014/34/EC) applies to all equipment used in potentially explosive atmospheres including protective systems. The name ‘ATEX’ is derived from the French title of this directive.
Electrical and mechanical equipment such as pumps, their motors and ancillary equipment are often required to operate in hazardous classified areas. In addition to the operational requirement of the equipment, it is essential that the equipment can be can be operated safely in a potentially explosive atmosphere. Pumps are assessed to be compliant to operate in a specific environment either by the manufacturer or by a third party, and a Declaration of Conformity or ATEX certificate has to be provided to confirm compliance.
IMPORTANT NOTE: ATEX certified equipment is not allowed to be installed in Australia without obtaining a Conformity Assessment Document (CAD). Conformity Assessment is a demonstration that specified requirements relating to a product, process, system, person or body are fulfilled. In the context of installing electrical equipment in a hazardous area, AS/NZS 60079.14 requires “assurance of conformity of equipment”.
II. Explosive Atmosphere
An atmosphere can become potentially explosive when it contains dangerous levels of flammable gases, mists or dusts. With a source of ignition, combustion spreads in an uncontrolled and catastrophic manner. The risk of explosion can be reduced by preventing the release or build-up of flammable substances and by eliminating sources of ignition.
Explosions can cause loss of life, serious injuries and significant damage to properties. Flammable gases, mists, vapours or combustible dusts, when present in sufficient concentration and mixed with air may explode if there is an ignition source such as a spark from electrical equipment. Preventing releases of dangerous substances, which can create explosive atmospheres, and eliminating sources of ignition are two ways of reducing the risk.
The ATEX directives distinguish between two different types of explosive atmospheres: GAS and DUST. Although it is not commonly appreciated, dusts such as flour or sawdust can be extremely dangerous and their handling requires special consideration. Areas within the two kinds of explosive atmospheres are each divided into three ‘safety’ sub-zones.
The following table shows the ATEX hazard zones and safety categories that equipment is required to meet to work in them:
ATEX Zone | Danger / Protection Level | Ex Safety Category Required | |
---|---|---|---|
Gas | Dust | ||
Zone 0 | Zone 20 | Constant danger (Very high). Explosive hazard always present. |
Category 1 equipment. |
Zone 1 | Zone 21 | Potential danger (High). Explosive hazard occasionally present during normal working practices. |
Category 2 or 1 equipment. |
Zone 2 | Zone 22 | Minor danger (Normal). Explosive hazard not likely or only for short periods |
Category 3, 2 or 1 equipment. |
III. ATEX Equipment Safety
Manufacturers must submit their products to conformity testing procedures by an outside agency known as a Notified Body. If equipment passes the tests carried out by the Notified Body and is deemed safe for use in one or more of the defined danger zones an Ex symbol may be displayed on the equipment to show that it has been approved to ATEX standards.
IV. Equipment ATEX information
ATEX equipment must bear the CE marking and this may be followed by the serial number of the Notified Body. The equipment will also bear the Ex logo and then a series of codes, to define its approval rating. An example for a hazardous area motor is shown below:
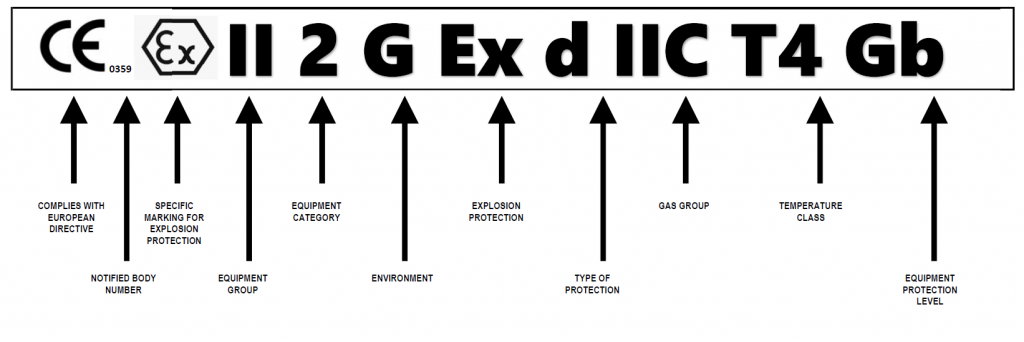
The ATEX designation consists of five elements:
- Equipment Group code and Safety category
- Atmosphere
- Protection type
- Gas group
- Temperature class
V. Equipment Group and Safety Category
There are two main Equipment Groups (designated by roman numerals) and these are sub-divided into Safety categories:
Equipment Group | Safety Category | ||
I | The equipment is suitable for use in underground parts of mines as well as those parts of surface installations endangered by firedamp and/or combustible dust | M1 | The equipment can be used in mines and powered safely when the explosive atmosphere is present |
M2 | The equipment can be used in mines but only when an explosive atmosphere is absent. If this is not the case, the equipment must be de-energised | ||
II | The equipment is suitable for use in all non-mining applications. | 1 | Protection level is very high and the equipment may be used safely when the explosive atmosphere is present continually or for long periods |
2 | Protection level is high and the equipment may be used safely when explosive conditions occur occasionally under normal operating conditions. | ||
3 | The equipment is safe for use when explosive atmospheres are not likely to be encountered under normal conditions and when they do, it will be for a short period only. |
Equipment for use in explosive atmospheres will normally be classified under Group II, in categories 2 or 3. To be suitable for Group II, category 1 or Group I certification, the equipment will require additional modifications.
When an equipment is rated for use in more than one environment there may be an Ex code for each zone.
VI. Equipment Protection Code
To eliminate the risk of electrical sparks, any equipment containing circuitry may contain additional features such as a sealed enclosure. In the Ex designation, these features are shown by one or more lower-case letters. Some examples relevant to pumps, motors and seal support systems are shown in the following table:
Symbol | Type of Protection |
d | Flameproof - The product incorporates mechanical features which are designed to contain an explosion and not allow any flame to escape. da and db versions are suitable for Zone 1 area use. The enclosure or junction box is constructed and certified as explosion protected according to the “Flameproof” standard. The “Flameproof” philosophy is that should an explosion occur within the enclosure, it will either be contained or the escaping flame will be cooled by a “flame-path” thus mitigating the risk of igniting an explosive outside atmosphere. |
db | Flameproof, suitable for Category 2, Zone 1 area use. |
eb | Equipment is designed and manufactured with components which prevent ignition sources being generated internally such as static discharges or high temperatures. Suitable for Zone 1 area use. The enclosure is constructed and certified as “Explosion Protected” according to the “Increased Safety” standard. The philosophy with Ex eb is to provide an impact resistant enclosure and also to ensure that its contents are certified such that they will never produce sparks, temperatures, or current creepage that could ignite the flammable atmosphere which may enter the enclosure. Ex eb rated enclosures are therefore explosion protected but are not “Flameproof". |
ec | The enclosure is constructed and certified as “Explosion Protected” according to the “Increased Safety” standard, but to a lesser level than eb. Suitable for Zone 2 non-sparking (formerly nA) hazardous areas. |
ia | Intrinsic Safety* (Permitted for Zone 0) depending on device category. |
ib | Intrinsic Safety* (sufficient for zone 1 (+2)) |
ic | Intrinsic Safety* (sufficient for zone 2 (+2)) |
* ‘Intrinsic safety’ means that the circuitry is low power and cannot transfer sufficient energy to ignite an explosive atmosphere. It is the only protection type allowed in Zone 0/20 environments.
VII. Gas Group
Chemical properties of explosive atmospheres such as molecular weight, upper and lower explosion limits and flame temperature affect the probability and severity of an explosion. Testing of these properties has resulted in the definition of design parameters including the maximum experimental safe gap (MESG), which is used to classify flammable gases for the design of electrical equipment in hazardous areas.
The MESG is a measurement of how easily a gas flame will pass through a narrow gap bordered by heat-absorbing metal. Every substance has its own combination of properties, however their MESGs rank in similar ranges, simplifying the selection of hazardous area equipment.
Each chemical gas or vapour used in industry is classified into a gas group.
Gas Group | Typical Substances |
IIC | Acetylene & Hydrogen |
IIB | Ethylene |
IIA | Propane |
VIII. Sources of Ignition
Potentially explosive atmospheres must be protected from sources of ignition such as friction sparks and high surface temperatures. It is important that the equipment does not exceed the auto-ignition temperature of the atmosphere where it is installed. high surface temperatures can result from, for example, mechanical friction in a bearing or simply because the pumped fluid is hot.
IX. Temperature Class
The Ex designation contains a code indicating the maximum possible surface temperature of the equipment. In some cases, the maximum surface temperature is written explicitly. Where it is dependent on the pumped fluid, it is marked with an X.
Since the surface temperature of a pump will also depend on the external, ambient temperature, the ATEX specification may also list an ambient temperature range for ‘safe’ operation, e.g. +1°C < Ta <40°C. Where this is not listed, it is assumed to be -20°C to +40°C.
ATEX temperature code | Maximum surface temperature °C |
T1 | 450 |
T2 | 300 |
T3 | 200 |
T4 | 135 |
T5 | 100 |
T6 | 85 |
X | Maximum temperature class depends on the temperature of the pumped fluid – limitations and a range of allowed temperature classes should be given in the documentation accompanying the equipment. |
X. Equipment Protection Level
Hazardous areas for the presence of potentially explosive substances are divided into zones. As reference to gases, vapors or mists, the relevant areas are classified in Zone 0, 1 or 2 according to international standard IEC 60079-10-1. For dust, the relevant areas are classified in Zone 20, 21 or 22 according to IEC 60079-10-2.
It is a fact that an explosion occurs when an ignition source is in contact with the explosive atmosphere. This situation must be absolutely avoided. In the most dangerous areas, in which the risk of explosion is caused by the presence of explosive gas or dust for long periods of time during the year, the equipment installed must have very high levels of protection. In the less dangerous areas, as the Zone 2 for gas and the Zone 22 for dust, you can use equipment with lower levels of protection.
Before the introduction of the ATEX Directive 94/9/EC, the protection method was the only compulsory requirement for the use of equipment in each respective area. For example, the use of a device in Zone 0 was only allowed if it is intrinsically safe "Ex ia". In Zone 1, the type of protection "Ex d" or "Ex e" could be used. With the introduction of the ATEX Directive 94/9/EC, the focus moved from the technical requirements of the equipment, identified by the way of protection, to the installation area. In practice, different equipment, apart from the type of protection, are classified into three categories for gases and others three for dusts, which correspond to the area in which they can be installed.
ATEX category | Substances | Protection Level | Zone |
---|---|---|---|
1G | Gas | Very high | Zone 0 |
2G | Gas | High | Zone 1 |
3G | Gas | Normal | Zone 2 |
1D | Dusts | Very high | Zone 20 |
2D | Dusts | High | Zone 21 |
3D | Dusts | Normal | Zone 22 |